گسکت مناسب فلنج یک عامل اساسی در بسیاری از فرآیندهای تولید است. گسکت در انواع و کاربردهای مختلفی وجود دارد. مواد سازندهی آنها براساس کاربردشان با یکدیگر فرق دارد و میتوان آنها را در قطارها، اتومبیلها، هواپیماها، قایقها، تجهیزات برقی، پمپها و دیگر موارد یافت. در این مقاله به بررسی انواع گسکت ها و کاربرد آنها پرداختهایم.
گسکت (Gasket) چیست:
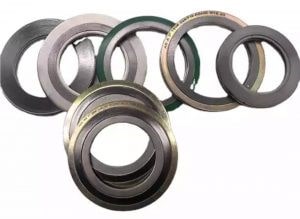
گسکت (Gasket) چیست
گسکت یا واشرها، نوعی درزبند مکانیکی الاستومری هستند که از ورق های تختی از جنس لاستیک، آلومینیوم، کاغذ، استیل، فولاد و… برای پر کردن فضای خالی بین دو اتصال یا فلنج که به دلیل فشار، احتمال نشتی دارند ساخته میشود. این تجهیزات تقریباً در تمام صنایع از جمله فرآوری مواد غذایی، پتروشیمی، دارویی، لوله کشیهای آب و گاز استفاده میشوند. به بیان ساده گسکت مناسب فلنج یک مهر و موم مکانیکی است که فضای بین دو یا چند سطح را جهت آب بندی و جلوگیری از نشت پر میکند.
گسکت ها معمولاً از مواد مختلفی ساخته میشوند، برخی از آنها شامل موارد زیر هستند:
- لاستیک
- چوب پنبه یا کاغذ
- فلز
- فوم و …
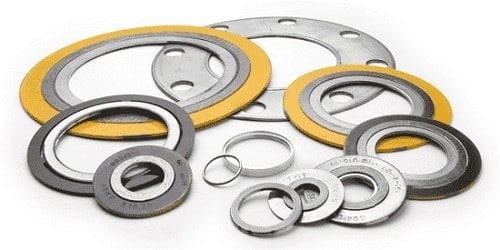
انواع مختلف گسکت (Gasket) ها
انواع گسکت های از لحاظ مواد سازنده آنها:
-
گسکت فلزی
این گسکت های بیشتر از آلومینیوم، مس، فولاد، نیکل، استنلس استیل یا برنج ساخته میشوند. این گسکت ها دارای مقاومت زیادی در برابر فشار و دما هستند، ولی معمولاً با مواد غیر فلزی نرمتر ترکیب میشوند تا آببندی سادهتر انجام گیرد.
-
گسکت سیلیکونی
سیلیکون به دلیل مقاومت بسیار بالایی که نسبت به دما دارد ماده بسیار مناسبی برای ساخت گسکت به شمار میرود. همچنین به دلیل مقاومت بالا در برابر اشعه ماوراء بنفش، برای استفاده در فضای آزاد نیز بسیار مناسب است. همچنین به خاطر مقاومت بالا در برابر شعله، گسکت ساخته شده از سیلیکون در صنایع الکترونیک و حمل و نقل نیز استفاده زیادی میشود.
-
گسکت های لاستیکی و پلاستیکی
به دلیل خاصیت کشسانی بسیار بالای لاستیک، این ماده برای ساخت بسیاری از گسکت ها استفاده میشود. لاستیک میتواند به سادگی تغییر شکل بدهد و درزها را بپوشاند تا آب بندی مناسب انجام شود. بعضی انواع پلیمرها نیز با خاصیتهای شبیه لاستیک معمولاً برای ساخت گسکت استفاده میشوند. در میان گسکت های لاستیکی و پلاستیکی میتوان به الاستومر ترموپلاستیکی، لاستیک ترموپلاستیکی و پی وی سی اشاره کرد.
انواع گسکت از لحاظ ساختار:
- گسکت جکت دار:
- در این نوع گسکت، انعطاف پذیری و کارایی گسکت های نرم (لاستیکی یا پلاستیکی) با مقاومت و دوامی که توسط یک پوشش فلزی ایجاد شده است ترکیب میشود. از انواع این گسکت میتوان به گسکت تک جکت و گست دوبل جکت اشاره گرد که نوع دوم در برابر فشار و دمای بالا و خوردگی مقاومت بسیار خوبی دارد. نوع دیگر، گسکت جکتی شیاردار است و همچنین میتوان به گسکت جکتی نوع فرانسوی اشاره کرد که هم داخل و هم خارج آن با فلز پوشش داده شده .
- گسکت سخت:
گسکت های سخت عموماً از فلز ساخته شدهاند و نسبت به گسکت های جکتی قیمت کمتری دارند. این گسکت ها در برابر دما و فشار مقاومت بالایی دارند، اما برای اینکه بتوان با گسکت های سخت به آببندی خوبی رسید به نیروی بسیار زیادی نیاز است، چرا که این گسکت ها انعطاف خوبی ندارند و با نیرو و انرژی زیادی باید آنها را هنگام اتصال محکم کرد.
انواع گسکت یا واشر فلنج:
- گسکت های غیر فلزی
واشرهای غیر فلزی میتوانند به راحتی و با فشار کم فشرده شوند. گسکت های غیر فلزی در دمای پایین استفاده میشوند اما نوع گرافیتیشان تا دمای ۵۰۰ درجه سانتیگراد قابل استفاده است. واشرهای غیر فلزی ارزانترین و در دسترس ترین نوع واشرها هستند. این واشرها همچنین به عنوان واشر نرم نیز شناخته میشوند.
متداولترین مواد مورد استفاده در این نوع واشرها شامل موارد ذیل است:
- گرافیت
- تفلون
- لاستیک
- PTFE
- فیبربدون آزبست فشرده شده (CNAF)
در تصویر زیر نمونهای از گسکت های CNAF و PTFE را مشاهده میکنید.
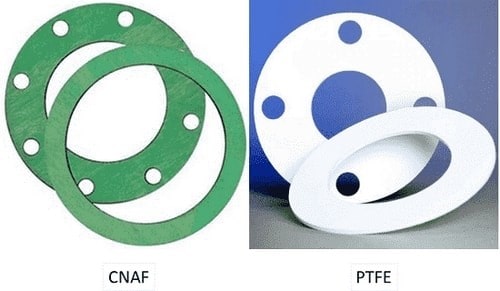
گسکت های CNAF و PTFE
گسکت-واشر بدون آزبست (Non Asbestos)
امروزه در صنعت گسکت تولیدکنندگان ترجیح میدهند جایگزین مناسبتری برای گسکت آزبستی ارائه بدهند. دلیل این انتخاب ماهیت خطرناک آزبست است. تولیدکنندگان ورق بدون آزبست را با استحکام مشابه به شیت آزبستی برای تعدادی از کاربردها تولید میکنند.
چرا ورق بدون آزبست ترجیح داده شد؟
چند سالی است که از ورق آزبست در صنعت استفاده میشود. افزایش نگرانیها در مورد خطرات سلامتی ناشی از آزبست باعث شده است که تولید کنندگان به دنبال جایگزینهای بهتر و مناسبتری باشند. در فرآیند تولید، آزبست فقط برای افرادی که به طور منظم در تماس مستقیم با الیاف آزبست هستند، نگرانکننده است. اما هنگامی که الیاف آزبست در گسکت قرار میگیرند استفاده از گسکت خطر خاصی ندارد.
با گذشت زمان الیاف آزبست نازک میتوانند در ریههای کارگرانی که در معرض کار کردن با آن هستند، انباشته میشود و منجر به مشکلاتی برای سلامتی بشود که ممکن است عوارض آن به اندازه سرطان شدید باشد. به همین خاطر تولیدکنندگان ورق بدون آزبست را برای ایمنی پرسنل معرفی کردند.
تفاوت بین گسکت آزبست و غیر آزبست
الیاف آزبست مستحکم هستند و میتوانند دماهای بالا را تحمل کنند. این الیاف نازک و بلند هستند. تولید کنندگان گسکت غیر آزبستی از موادی مثل گرافیت، PTFE و آرامید به عنوان الیاف تقویتکننده در گسکتها استفاده میکنند. این الیاف دارای خواصی مانند مقاومت در برابر حرارت، مقاومت در برابر دما، مقاومت شیمیایی و غیره هستند. خواص این الیاف تضمین این موضوع است که عملکرد گسکتها با قطع استفاده از آزبست تحت تأثیر قرار نمیگیرد. گسکتهای آزبستی از الیاف سیلیکات ساخته میشوند در حالی که ورق بدون آزبست با استفاده از مواد کربنی یا مواد آلی ساخته میشوند. ورقهای آزبست نسبتاً ارزانتر از ورق بدون آزبست هستند. سازندگان گسکت به طور مداوم با مواد مختلف کار میکنند تا به مشتریان خود شیت گسکت غیر آزبستی نوآورانه و بسیار مؤثری ارائه بدهند. این نوآوری میتواند باعث شود که مشتریان با توجه به نیاز خودشان بتوانند ورق بدون آزبست سفارش بدهند. شیت گسکت غیر آزبستی را با استفاده از الیاف آلی، الیاف آرامید، NBR و الیاف معدنی تولید میکنند. این ورقها را میتوان در جاهایی استفاده کرد که به مقاومت در برابر روغن یا آب نیاز است. به طور کلی شیت گسکت غیر آزبستی در دستگاههای کم فشار، ترانسفورماتورها و کمپرسورها استفاده میشود. آنها همچنین در روکش سوپاپها و موتورهای احتراق داخلی که در آن اجزای به راحتی قابل تغییر شکل هستند به کار میروند. این روزها تولیدکنندگان ورق بدون آزبست را به این دلیل هم ارائه میدهند که ممکن است ویژگیهای خاصی مثل آزبست داشته باشد یا حتی برتریهایی نسبت به آن. از آنجایی که کربن یا مواد آلی پایه ورق بدون آزبست است استفاده از آنها نسبت به ورق آزبستی ایمنتر است.
مواد غیر آزبستی که بهجای آزبست استفاده میشوند چه هستند؟
این مواد در حال حاضر معمولاً از الیاف آرامید (کولار)، کربن و سایر الیاف غیر آلی تشکیل شدهاند که به نوبه خود با پلیمرهای مختلف برای برآوردن کاربردهای متفاوت ترکیب میشوند: مثلاً با لاستیک نیتریل برای مقاومت در برابر سوخت و روغن، با پوشش گرافیت برای مقاومت در برابر بخار، با PTFE برای مقاومت شیمیایی خیلی خوب و با EPDM برای کاربردهایی در صنایع آبهای آشامیدنی ترکیب میشوند.
صنایع رایج در استفاده از ورق بدون آزبست:
– نفت و گاز
– مواد و پروسههای شیمیایی
– صنعت پتروشیمی
– صنایعی با حجم تولید بالا
- گسکت های فلزی
این واشرها همچنین به اسامی حلقهای یا RTJ معروف هستند. واشر فلزی در فشار بالا استفاده میشود، همچنین میتوان از آنها در درجه حرارت بالا استفاده کرد. در هنگام استفاده از نوع فلزی، برای عملکرد صحیح به فشار بالا نیاز است تا واشر به درستی بین سطوح قرار گیرد.
برای ساخت واشر فلزی از مواد مختلفی استفاده میشود که شامل موارد زیر هستند:
- آهن نرم
- فولاد کم کربن
- استیل ضد زنگ
- مونل
- اینکونل
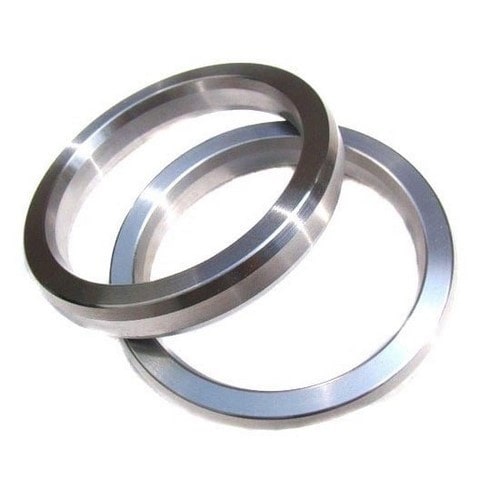
گسکت های فلزی
گسکت رینگی Ring Joint Gasket:
گسکت های رینگی براساس استاندارد، API 6A و ASME B16.20 ساخته میشوند و جهت اتصال فلنجهای نوع (Ring Type Joint:RTJ) منطبق بر استانداردهای API 6A ، ASME B16.5 ،MSSSP-44 استفاده میشود. جنس آنها معمولاً از استنلس استیل ۳۰۴ یا ۳۱۶ و یا آهن نرم (Soft Iron) است و دارای مقطع بادامکی (Oval) و یا ۸ ضلعی (Octagonal) است. قابلیت تحمل فشار و دمای بالایی رو دارند و اکثرا در محیطهایی که عامل خورندگی وجود دارند استفاده میشوند. همواره توصیه میگردد که سختی جنس گسکت های رینگی از سختی فلنجهای مورد نظر کمتر باشد گسکت رینگی پرکاربردترین گسکت فلزی است که از فولاد یا آلیاژ نرم ساخته میشود و به دلیل مقاومت بالایی که در برابر فشار و دما دارند، برای آببندی یا درزبندی فلنجها در صنایع مختلف به کاربرده میشوند.
بیشتر بخوانید: استاندارد ابعادی و آلیاژی فلنج های فولادی چگونه است؟
گسکت های رینگی در چهار مدل تولید میشوند که عبارتاند از:
- گسکت رینگی R:
گسکت رینگی R
گسکت های رینگی یکی از پرکاربردترین نوع هستند که در فلنج هایی که از سطح صاف یا برجسته ساخته شدهاند، استفاده میشوند. گسکت نوع R در مقطع هشت ضلعی و بیضی برای آب بندی فلنجها استفاده میشود. از این نوع گسکت برای کلاس کاری بین 900 تا 1500 استفاده میشود.
- گسکت رینگی RX:
گسکت رینگی RX
از گسکت رینگی RX برای آببندی شیارهایی که ساختاری شبیه به خود دارد استفاده میشود. غالباً از این نوع گسکت رینگی در فلنج های سرچاهی و برای مواردی که نیاز به تحمل ضربه، فشار و ارتعاشات بالا باشد، استفاده میشود. این گسکت ها میتوانند تا کلاس کاری 1500 مورد استفاده قرار بگیرند.
- گسکت رینگی BX:
گسکت های BX برای کلاس کاری بین 5000 تا 15000 مورد استفاده قرار میگیرند و نسبت به انواع دیگر گسکت ها قطر بیشتری دارند.
گسکت اسپیرال وند Spiral wound Gasket:
این گسکت ها دارای یک لایه از جنس فولاد ضد زنگ و یک لایه پرکننده از جنس آزبست یا تفلن یا گرافیت است که با مقطع (V)وی شکل به صورت فشرده دور هم پیچیده شده است. ضخامت این نوع از گسکت ها برای تمام اندازهها و کلاسها یکسان است. این گسکت ها از ترکیب یک فلز شکل داده شدهی سیمی و مواد نرم پر کننده تشکیل شده است. شکلشان هنگامی که در بین دو فلنچ فشرده میگردند تأثیر زیادی در آببندی دارند. این نوع لایهها ممکن هست دارای رینگ داخلی یا خارجی باشند که رینگ داخلی میزان خوردگی فلنچ را کاهش داده و از اجزای آببندی محافظت میکند، و رینگ خارجی برای صحیح نصب کردن لایی کاربرد دارد. معمولاً جنس این رینگها فولادی و ضخامت آنها ۳.۵میلیمتر است. مقاومت و ارتجاعی بودن گسکت های مارپیچی عواملی هستند که این نوع از گسکت ها را گزینهی مناسب برای استفاده در کاربردهای متنوع متمایز ساخته است
واشر زخم اسپیرال:
گسکت زخم مارپیچ ترکیبی از مواد فلزی و پرکننده را تشکیل میدهد. به طور کلی این واشر دارای یک فلز (معمولاً از جنس استنلس استیل) است که به صورت یک مارپیچ دایره ای به بیرون منتقل میشود (اشکال دیگر ممکن است) با مواد پرکننده (گرافیت انعطاف پذیر) با همان شیوه زخم میشود اما از طرف مقابل شروع میشود. این منجر به لایههای متناوب پرکننده و فلز میشود. مواد پرکننده در این واشرها بهعنوان عنصر آببندی عمل میکنند. واشرهای زخم جرمی برای فلنجهای ASME ، DIN ، JIS طراحی شدهاند. ً انواع واشر زخم مارپیچ: R / IR / CG / CGI
- گسکت های کامپوزیت یا نیمه فلزی
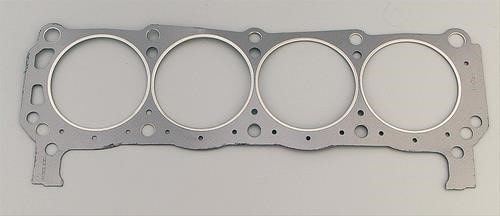
گسکت های کامپوزیت یا نیمه فلزی
گسکت کامپوزیت یا نیمه فلزی، ترکیبی از مواد فلزی و غیر فلزی هستند که بر اساس کاربرد ترکیبهای مختلفی از مواد سازنده در آنها استفاده میشود. گسکت های کامپوزیت در فشار و دمای مختلفی مورد استفاده قرار میگیرند.
این نوع از گسکت ها در مقایسه با واشرهای فلزی از نظر اقتصادی مقرون به صرفه تر هستند اما هنگام نصب دقت بیشتری لازم دارند. گسکت زخم اسپیرال و کامپروفیل در دستههای کامپوزیت کاملاً شناخته شده هستند.
گسکت کامپروفایل Camprofile:
گسکت های کامپروفایل معمولاً از یک رینگ فلزی شیارخورده به همراه لایههای انعطافپذیر مانند گرافیت در دو طرف آن تشکیل میشود و باوجود انعطاف مناسب در برابر تغییرات دما و فشار، این مدل از گسکت ها انتخاب مناسبی برای مبدلهای حرارتی به حساب میآیند. علاوه بر این امکان استفاده مجدد از این گسکت ها پس از ترمیم و بازیابی وجود دارد. کامپروفایل ها خودشان را در صنعت ثابت کردهاند. این گسکت ها در ماشین آلات قدرتمند صنعتی و محورهای اولیه تأسیسات اتمی یافت میشدند. استفاده دیگر این گسکتها در واحدهای مبدلهای حرارتی در کاربردهای اتمی است. همچنین در صنایع نفت و گاز و پتروشیمی کاربرد دارند. شوند. جنس شان از یک فلز در مرکز گسکت که معمولاً استنلس استیل است و آببند در دو طرف که بر اساس نوع سرویس میتواند گرافیت، تفلون یا از جنس فلز باشد.
گسکت اسپیرال وند Spiral wound Gasket :
این گسکت ها دارای یک لایه از جنس فولاد ضد زنگ و یک لایه پرکننده از جنس آزبست یا تفلن یا گرافیت است که با مقطع (V)وی شکل به صورت فشرده دور هم پیچیده شده است. ضخامت این نوع از گسکت ها برای تمام اندازهها و کلاسها یکسان است. این گسکت ها از ترکیب یک فلز شکل داده شدهی سیمی و مواد نرم پر کننده تشکیل شده است. شکلشان هنگامی که در بین دو فلنچ فشرده میگردند تأثیر زیادی در آببندی دارند. این نوع لایهها ممکن هست دارای رینگ داخلی یا خارجی باشند که رینگ داخلی میزان خوردگی فلنچ را کاهش داده و از اجزای آب بندی محافظت میکند، و رینگ خارجی برای صحیح نصب کردن لایی کاربرد دارد. معمولاً جنس این رینگها فولادی و ضخامت آنها ۳.۵میلیمتر است. مقاومت و ارتجاعی بودن گسکت های مارپیچی عواملی هستند که این نوع از گسکت ها را گزینهی مناسب برای استفاده در کاربردهای متنوع متمایز ساخته است
واشر زخم اسپیرال:
گسکت زخم مارپیچ ترکیبی از مواد فلزی و پرکننده را تشکیل میدهد. بطور کلی این واشر دارای یک فلز (معمولاً از جنس استنلس استیل) است که به صورت یک مارپیچ دایرهای به بیرون منتقل میشود. با مواد پرکننده (گرافیت انعطاف پذیر) با همان شیوه زخم میشود اما از طرف مقابل شروع میشود. این منجر به لایههای متناوب پرکننده و فلز میشود. مواد پرکننده در این واشرها به عنوان عنصر آب بندی عمل میکنند. واشرهای زخم جرمی برای فلنجهای ASME ، DIN ، JIS طراحی شده اند. ً انواع واشر زخم مارپیچ: R / IR / CG / CGI
گسکت جکتی:
گسکت جکتی شامل یکلایهی بیرونی فلزی به همراه پرکنندههای فیبری فشرده فلزی یا غیرفلزی میشوند. ماده پرکننده به گسکت مقاومت میبخشد، درحالیکه جکت فلزی از پرکننده و فشارهای خارجی، دما و خوردگی محافظت میکند. محدوده وسیعی از مواد برای شرایط مختلف دمایی و خوردگی وجود دارد، این نوع واشرها در محدوده وسیعی از اندازهها و حالتهای مختلف تولید میشود. کاربرد این گسکت ها در مبدلهای حرارتی، پمپها و شیرها است؛ بازیابی خواص این گسکت ها محدود است. این گسکت ها به سطح پرداخت شده نرم فلنج نیاز دارند و برای فلنجهای سطح برجسته مورداستفاده قرار میگیرند.
نکات مهم در انتخاب واشر مناسب:
- طول عمر گسکت
- سازگاری مواد سازنده گسکت با مایع
- توانایی تحمل فشار و دمای آن
- درک درست از نیازها و الزامات در مورد کاربرد گسکت ها قبل از انتخاب آن بسیار مهم است.
- از مواردی که باید به آن توجه کرد این است که گسکت بتواند در یک بازه قابل قبول کارایی خود را در برابر تمام نیروهای عملیاتی درگیر حفظ کند.
چه عواملی بر عملکرد واشر تأثیر دارد؟
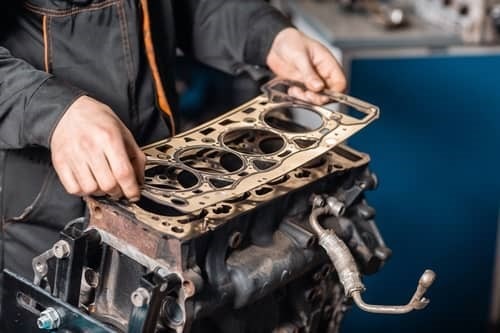
چه عواملی بر عملکرد واشر تأثیر دارد؟
هشت عامل مهم در هر گسکت که برای رسیدن به هدف و عملکرد ایدهآل باید داشته باشد، عبارت است از:
- عدم نفوذپذیری: گسکت نباید بعد از اتصال تحت فشار داخلی یا خارجی متراکم شود تا بتواند به بهترین شکل از نشت جلوگیری کند.
- تراکم پذیری: گسکت باید تحت فشار متراکم شود و نواقص اتصالات را برطرف کند.
- مقاومت در برابر نازک شدن: گسکت در هنگام اعمال نیرو و دما نباید ضخامت خود را از دست دهد. این موضوع باعث میشود فضای بین اتصالات باز شده و پیچ و مهرهها شل شوند و در نهایت سبب ایجاد نشت میشود.
- انعطافپذیری: اتصالات در محل گسکت به طور معمول ثابت هستند اما
تحت تاثیر دما و فشار مقدار کمی حرکت ایجاد میشود.گسکت باید قادر به جبران چنین حرکاتی باشد. - تعویض آسان: واشر باید پس از استفاده به راحتی قابل جدا شدن است.
- مقاومت شیمیاییش: گسکت باید در برابر خوردگیها و تأثیرات مواد شیمیایی مقاومت کند.
- مقاومت در برابر دما: واشر باید قادر به تحمل اثرات حداکثر و حداقل دما در طی فرایند و دمای خارجی و داخلی باشد.
- ضد خوردگی: واشر نباید باعث خوردگی فلنج شود.